EoM
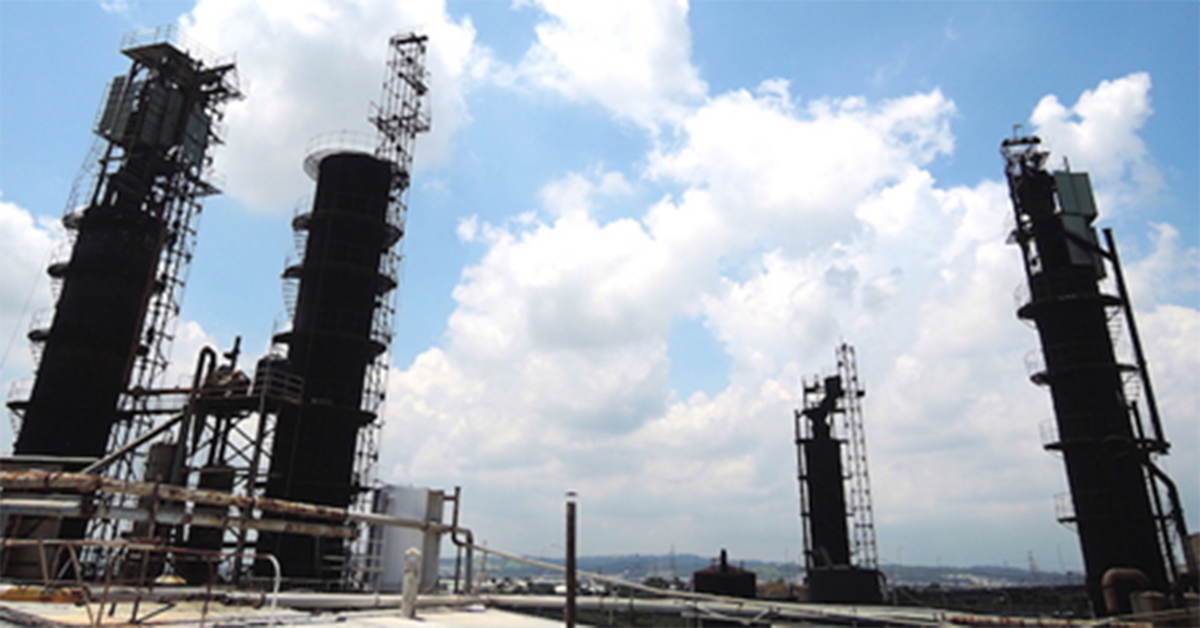
Case Study
This case is a company specializing in the production of nano-grade colloidal calcium carbonate. The products can be used as inorganic additives for polymers such as rubber, plastics and coatings, and are widely used in tires, wires and cables, PVC products, paints and other fields. The main products are colloidal calcium carbonate CC, CCR, TDD, OT, etc., with different particle sizes, different surface treatment agents and other specifications, suitable for different polymer materials. Since 2019, it has actively promoted Industry 4.0, through the IoT technology, real-time understanding of process information, and transformation to smart manufacturing. In response to the promotion of domestic energy conservation and carbon reduction, and environmental protection policies, an energy management system is established to monitor the power consumption of equipment, and to promote water conservation, electricity conservation, energy conservation and other environmental protection policies, and move towards the goal of cleaner production and green production.
Challenges and Countermeasures
The factory is located in Taichung, which has a history of more than 40 years and covers an area of 30,000 square meters. The equipment in the factory is scattered and the distance is far away, which is difficult to manage in a unified manner. In addition, the old system cannot capture the equipment in time. There are dozens of process motors in each area that are produced 24 hours a day. It’s not timely enough and requires a lot of manpower to inspect for troubleshooting, which indirectly affects the monthly production volume and the generation of intangible costs. In the case of a major transformation, it is possible to visualize the presentation of data and solve the pain points as the primary goal.

Research & Solution
In order to save the cost of pulling cables and complicated pipeline construction, All the data are transmitted with IOT wireless sensors by combination of BLE and SUB1G so that analyze the operation status and power consumption of the process motor, ice water host and CO2 windmill. And abnormal signals are sent back to the cloud and mobile APP. On-site personnel can get the warning messages at first time and monitor the real time data with 3Enlighten cloud system of EoM power monitoring. In addition, There are the benefits that the analysis tools solve the problem of machine failures and energy waste with traditional labor management and aging machines. The contribution of SaaS service with immediacy and sharing improves environmental safety, production management and cost reduction, and achieve the goal of smart factories. It makes a big step forward.

實際應用及產出成果
It took about 120 minutes from the problem discovered and reported to restart the mechine. Since the smart system has been installed. Sending early warning to the mobile APP immediately as faults or unexpected shutdowns of the process motor. The time of the process is decreased from 120 to 45 minutes.

There are three systemday(day shift middle shift night shift) in the factory. It almost doesn’t need manual adjustment and operation after putting the raw material in machine at 10PM in night shift. It needs to have one more person for inspections to make sure all equipments are in normal operation. However, the quality of the inspections were not good enough. Therefore, we installed the SaaS function so that it’s easy to get long-term data as a reference to establish normal and abnormal parameters of each equipment. Unnecessary manpower can be saved with real-time notification system. In addition to, it can save 5 manpowers in the day shift and expect to reduce the annual cost of NT$400,000.
In the past, the maintenance and replacement of machines just only rely on the usage time and the recommendations from the provider. It provides the analyzing and diagnosis to check the aging equipments with 3Enlighten cloud system. It is found that because the raw materials in the process need to be cooled by cooling water, the ice water main machine in the factory area is turned on for more than 12 hours a day, and the usage time has exceeded 20 years. After the diagnosis and analysis, it wasted the cost over NT$160,000 per year due to the aging equipment. Moreover, it can reduce the power comsumption of about 40% per year by replacement peripheral parts of the ice water and AI system. The ROI(Return of investment) is just only 4 years.

The conclusions
本次透過EoM電力監測系統帶來的效益:
Reduce equipment troubleshooting time from 120 minutes to 45 minutes.(which is 62.5% reduction)
Saving over 5 manpowers with digitization,(which has NT$400,000 benefit per year)
Reduction of power comsumption with AI energy-saving systems( over NT$500,000 per year )
